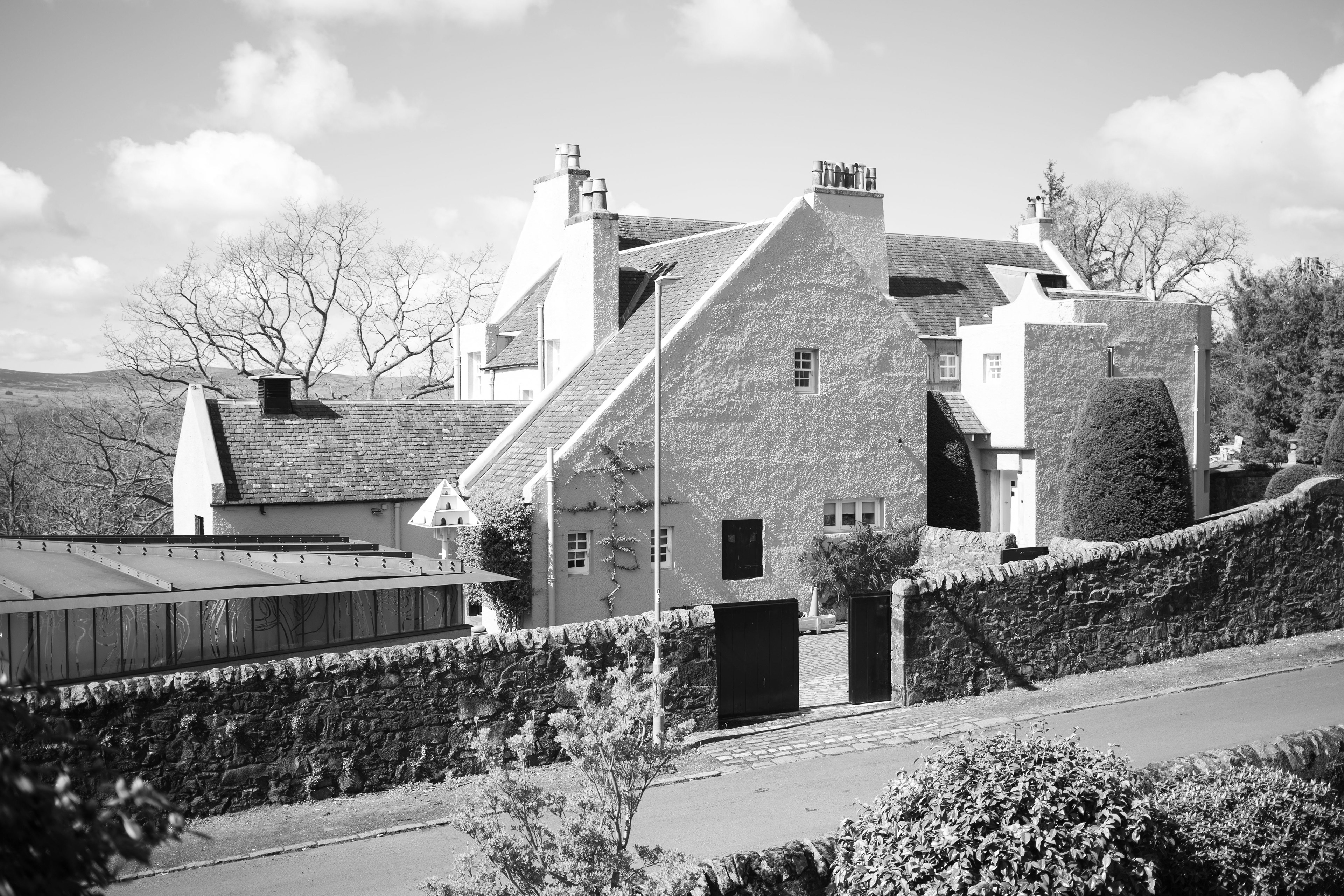
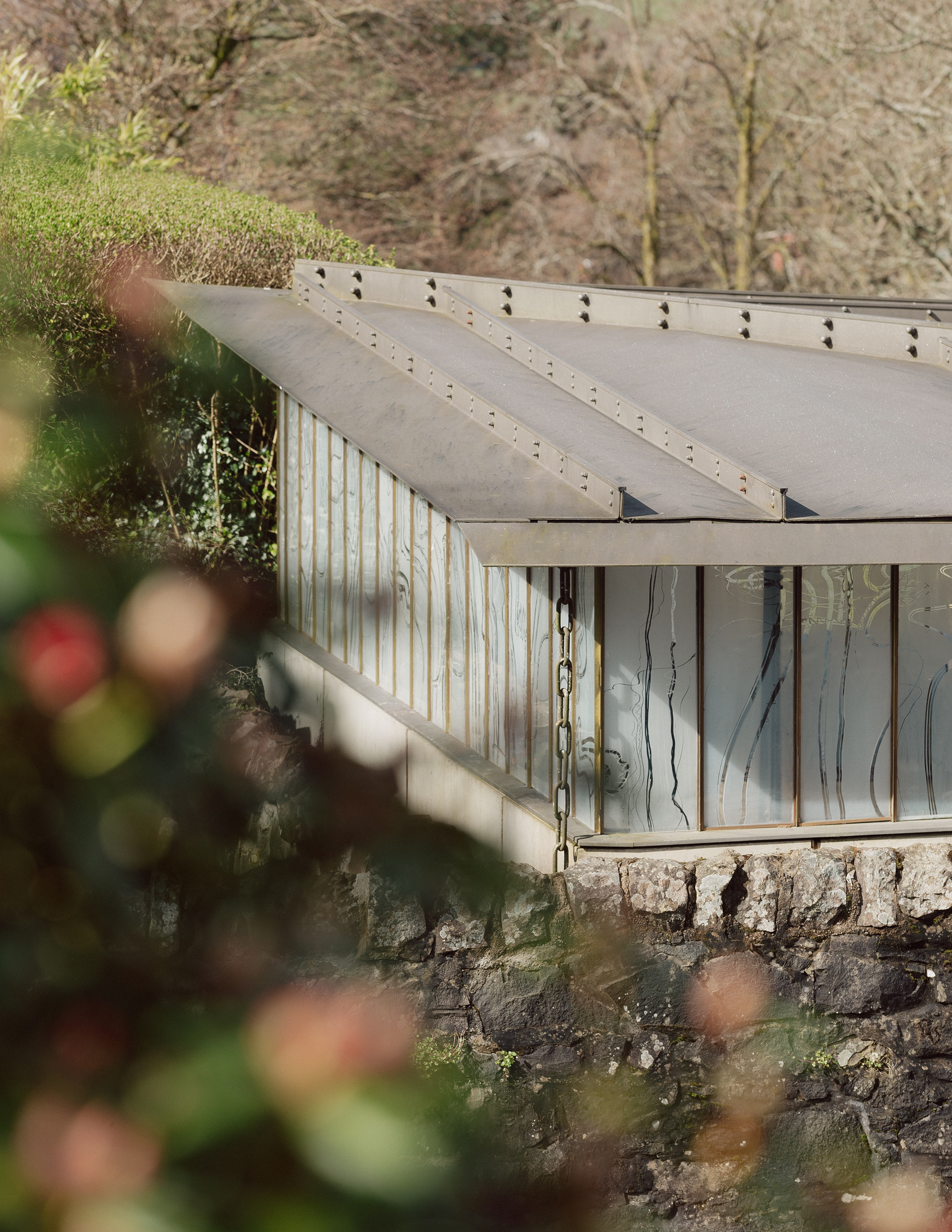
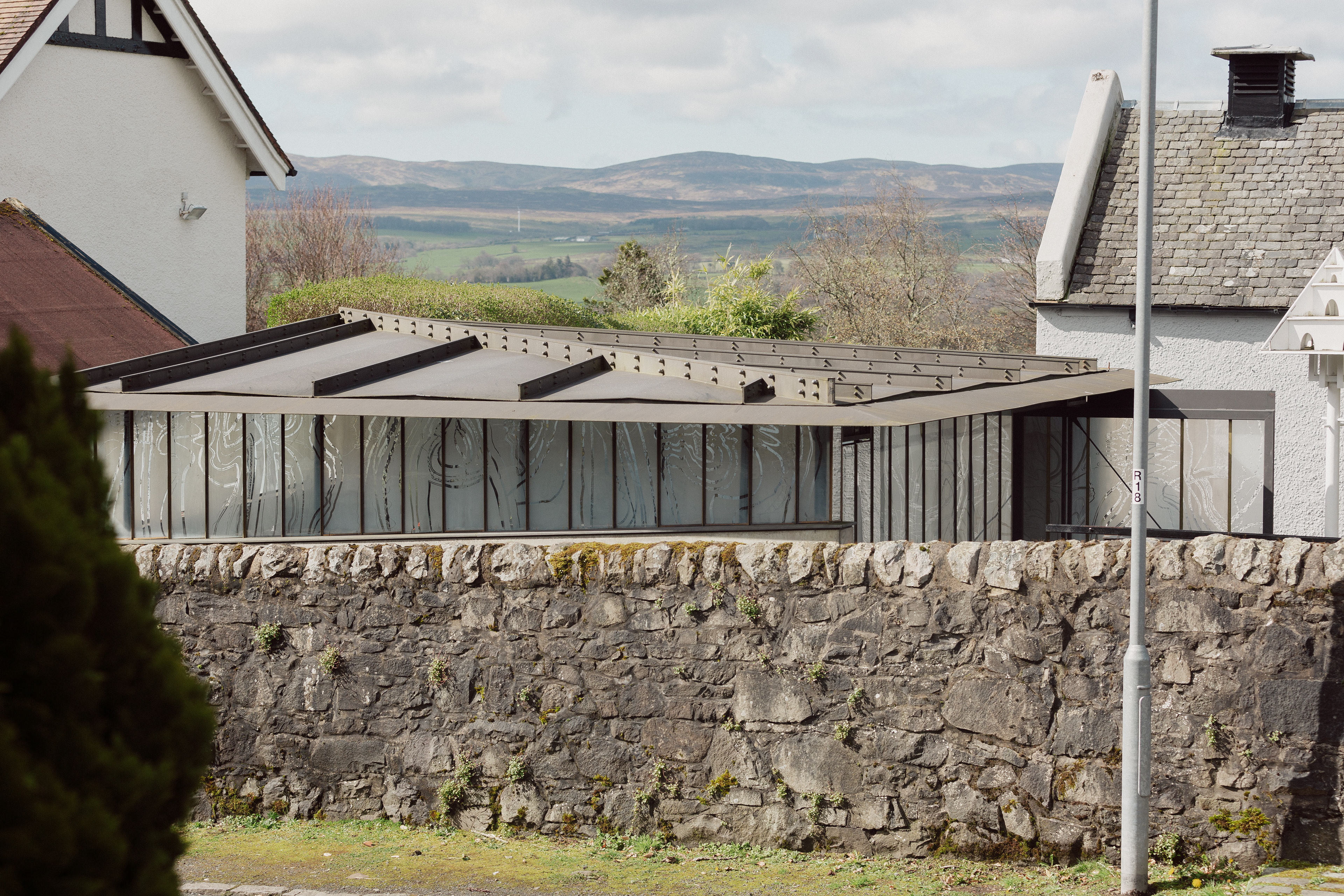
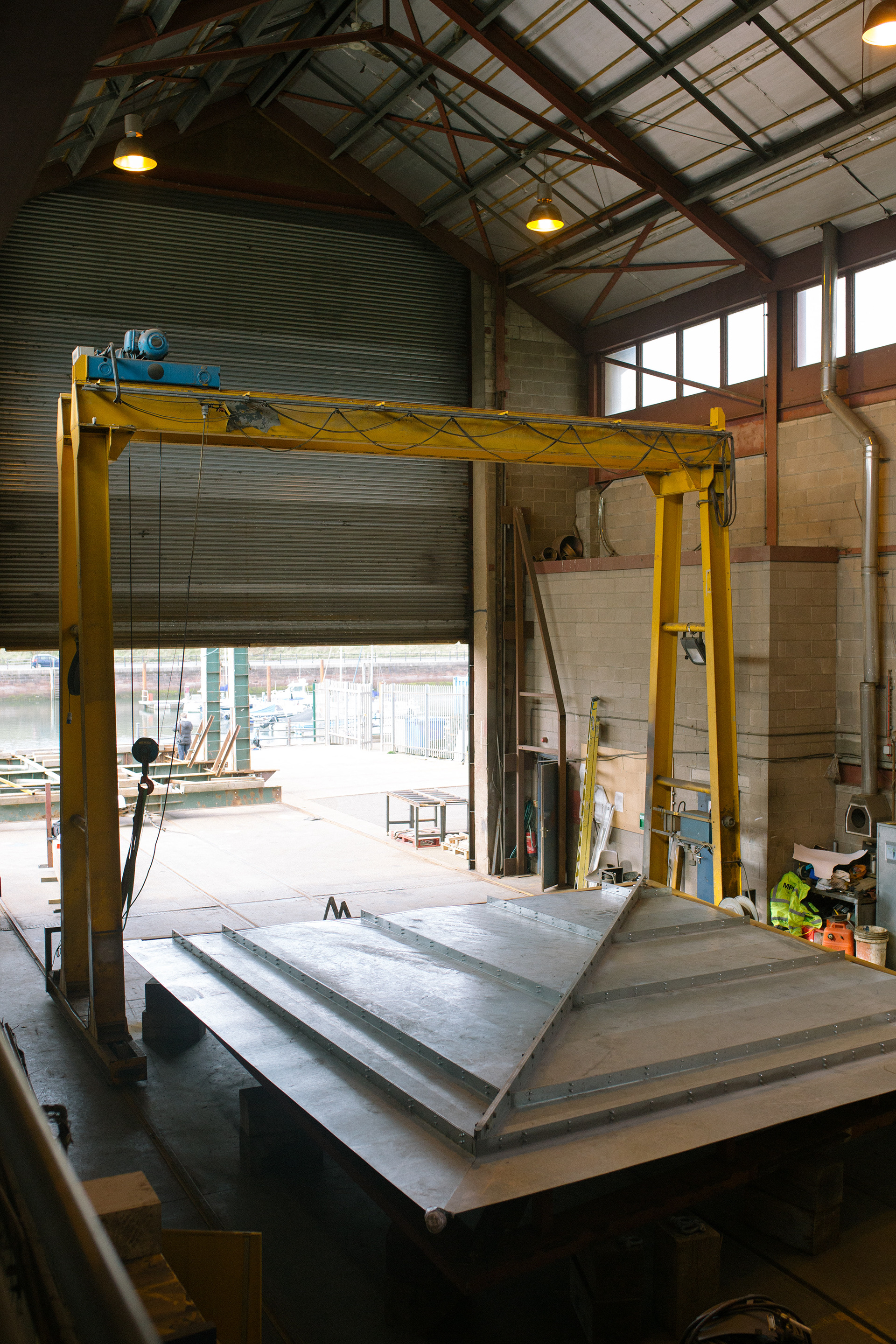
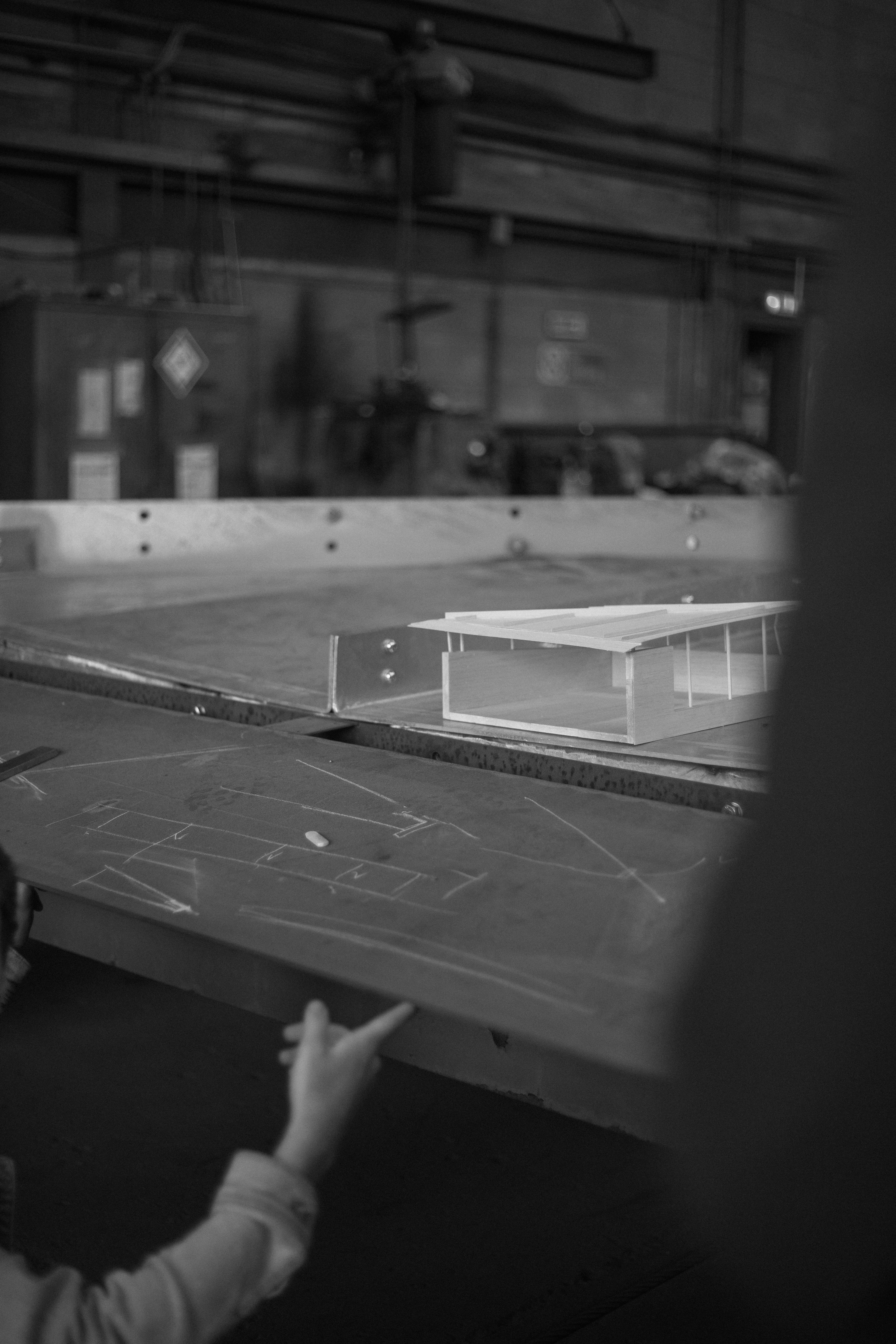
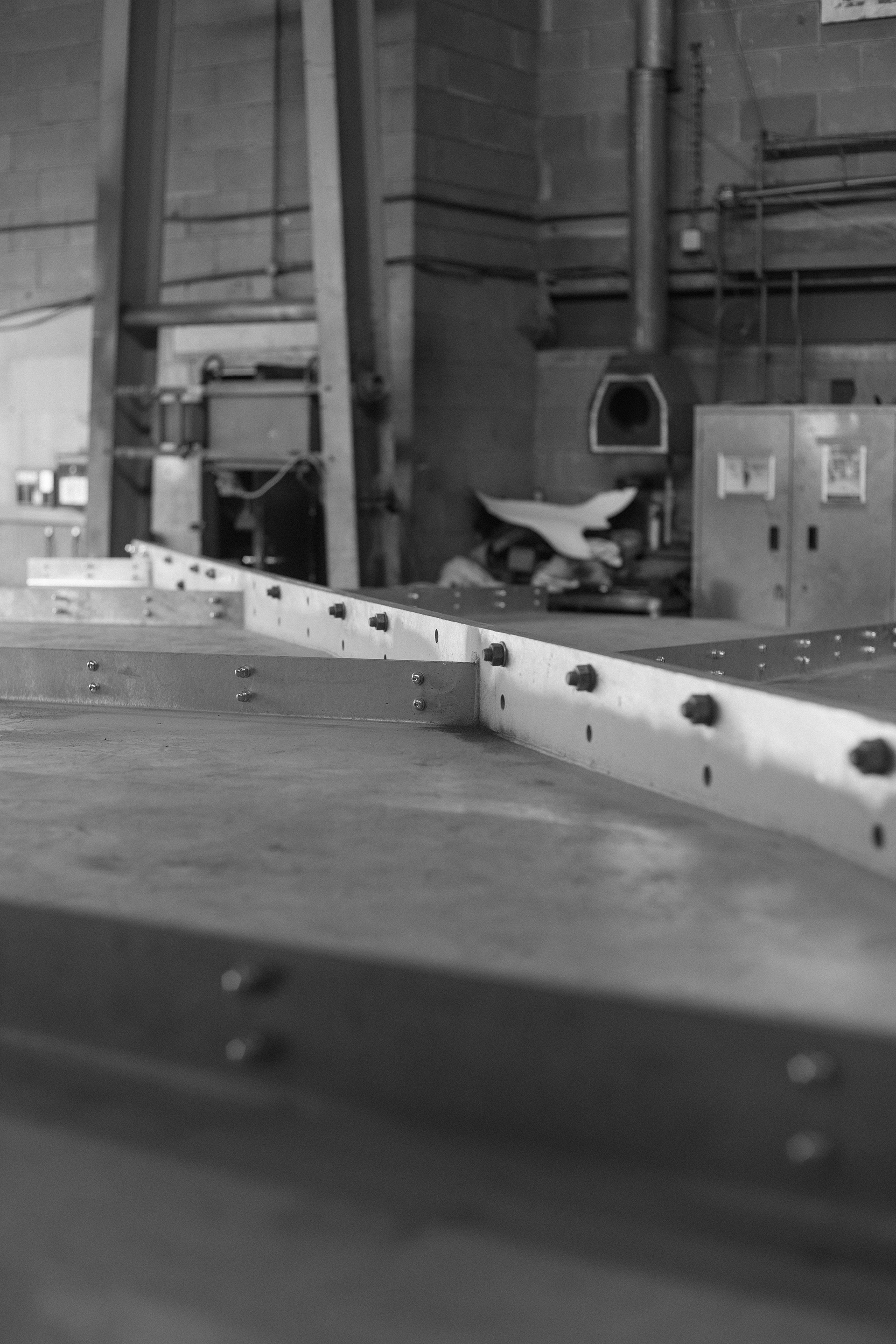
WINDYHILL MOTOR GARAGE, KILMACOLM
Bard
Windyhill was the first prototype house design from world renowned Scottish architect Charles Rennie Mackintosh and is his last remaining project that is still used for its original purpose. Part of the charm of the house in comparison to other examples of his work is that it remains a working home, a dwelling house. Completed in 1901, the house was pivotal in Mackintosh’s artistic and creative development.
BARD were commissioned by Windyhill’s proprietor to design a high quality garage structure adjacent to the building, replacing a c. 1980s car port. The process required careful observation and analysis of Mackintosh’s design intentions; leading later to our assistance in the restoration of a number of elements across the property inside and out.
The design is an abstraction and continuation of the narratives of the site’s original author, choosing not to imitate Mackintosh’s artistic language but to respond to the concerns and advances of the present time.
The new garage references Mackintosh’s own hand and those from which he drew. His botanical study ‘Sea Pink, Holy Island’, where he labels ‘seed’, ‘bud’ and ‘flower’ adjacent to the various elements of the plant – completed the same time as the house in July 1901 – presents ideas similar to those which percolate Windyhill, serving as a relevant narrative from which to construct a contemporary architecture.
The resultant structure is comprised of 3 main elements: a concrete basin, where ground slab and wall are one; articulated tapering steel stanchions which grow to support a plate steel roof; and hand-finished translucent glass which wraps around the perimeter, enclosing the construction in an atmosphere akin to petrified fog. The motor garage represents the established seed or bud, ahead of its future ‘bloom’.
The roof structure does not have conventional bracing, and its main material is both its skin as well as structure being 6mm plate steel. The precast masonry elements were lifted into place by crane and installed in a single day. Followed by the steel tapering stanchions and enormous delta shaped roof pieces which took just one further day for installation. This was made possible by meticulous drawing, model testing, constant dialogue with contractors, fabricators and structural engineer and by reviewing the prefabricated elements as they were being made.
The roof is supported on 15 bespoke individual stanchions, where the webs of T-section are sliced down to a taper, and separated by bushes to allow a gap between the back-to-back T-section. The tapering refers to the transformation from base to tip, akin to Mackintosh furniture. Standard steel sections were transformed into something extraordinary, much like Mackintosh did by bending flange and webs on T-sections at his Glasgow School of Art to support timber roof trusses.
In this case the enormous roof was considered in two triangles, pre-fabricated in a workshop in Maryport by shipwrights. The sheets were bent/ folded to help with tensile strength with the uprights / ribs giving visible presence to the structure above. The roof and all visible steelwork were designed to be immediately the buildings own skin – no coverings or obfuscation. Initially, the use of corten steel was considered due to its longevity and its contemporary appearance. It was decided that this would not sit well with Mackintosh’s building in relation to its colours and tones.
Therefore, mild steel, hot dip galvanised was chosen with a Micaceous Iron Oxide (MIO) coating to blend with the tones of the house, and add an element of intrigue to the finished result.
Each “tray” of the roof was individually galvanised once they were shaped by the profilers, and all the holes pre-cut in the correct positions ready for the mechanical fixings. These were then assembled and the steelwork further coated in MIO. The roof was disassembled and loaded onto a tilting trailer and transported from Cumbria to Inverclyde ready for assembly. The steelwork has a beautiful quality to it, it is thin and elegant as well as visceral and honest in the expression of its parts. The sheet surface is both skin and structure. The stanchions are in constant compression and working in unison. All of this has only been possible due to the possibilities of galvanising to allow the investment in this material to perform to standards, and ensure longevity to the structure.
Photographs © Alex James-Aylin